Page 3 of 3

Posted:
Sat Mar 23, 2013 1:42 am
by snaggletooth
thats awesome man. haas makes a nice machine. i use a haas super mini mill 2 every day as my main machine these days but my last shop was a production company of hydraulic motors and gear boxes. i got to use some sweet machines man. a verticle lathe with live tooling as tall as the warehouse that i had to load with a crane. turning 300lb motor body housings for the most part. also a 5 axis milling machine that was sweet but you had to use mastercam to program it because it gets crazy.
now i just do little aluminum prototyping stuff. nice because my back doesn't hurt as much, but keep it up man CNC is a great way to make money. I'm only 23 and i'm already pulling close to 40k a year.

Posted:
Sat Mar 23, 2013 4:54 am
by 92civicEGsedan
snaggletooth wrote:thats awesome man. haas makes a nice machine. i use a haas super mini mill 2 every day as my main machine these days but my last shop was a production company of hydraulic motors and gear boxes. i got to use some sweet machines man. a verticle lathe with live tooling as tall as the warehouse that i had to load with a crane. turning 300lb motor body housings for the most part. also a 5 axis milling machine that was sweet but you had to use mastercam to program it because it gets crazy.
now i just do little aluminum prototyping stuff. nice because my back doesn't hurt as much, but keep it up man CNC is a great way to make money. I'm only 23 and i'm already pulling close to 40k a year.
I wished we had a 5 axis mill in class I could make some crazy stuff then. We just got a 3 axis CNC mill and a few manuals but we upgraded one manual to where it will cut pockets and circles and lines it's pretty sweet and our teacher is trying to get the college to get another CNC mill and a few more machines which would be awesome. I like running the manuals more since you can make something and be like yeah I made that and be proud of it unlike on the CNC where you make the program and put it in and it make the part for you but we don't have master cam yet so we have to manually write the program and since I already took both CNC classes I won't be able to learn master cam

Posted:
Sat Mar 23, 2013 4:45 pm
by snaggletooth
my old boss just gave me a copy from the machine shop and i learned how to use mastercam that way. i do most of my programming on the spot now, i just type them up in microsoft note pad and use a usb port to transfer the program, but mostly because my new job has bobcam instead of mastercam and it sucks. i feel yea on the manual machining vs. CNC thing but at my new job i use ten thousandth diameter endmills to make micro groves for injection molds for gold micro-connectors with tolerances of .001"+/- and basically without CNC fuck that, but simple shapes i just use our bridgeport old manual mill. thats fucking awesome that you have a retrofitted manual that can do radius's, that would make a world of difference. stick with it man, and when you get to do crazy multi axis machining you'll appreciate CNC more just the ability to make fucking anything no matter how small.

Posted:
Sun Mar 24, 2013 12:35 am
by 92civicEGsedan
If we had a 5 axis I'd port my head haha


Posted:
Sun Mar 24, 2013 9:56 pm
by snaggletooth
i bored out my moped and got a little 40cc motor going 60 miles an hour. its 70cc now i think, but you don't get to fuck around with the machines much just because of how high the over head is on machine shops. you know the saying if the spindle aint turning the shop aint earning.

Posted:
Wed Mar 27, 2013 3:25 pm
by 92civicEGsedan
im planning on making a stroker kit with aluminum cylinder for my weedeater motor and and supercharger for it lol just as a prototype for my lawn mower engine and then to the 4 wheeler engine and eventually if the prototype S/C works ill make one for my car lol

Posted:
Thu Mar 28, 2013 1:23 am
by 92civicEGsedan
Started on the velocity stack tonight on the manual lathe now I just need to Finnish boring it out and to round off the corners
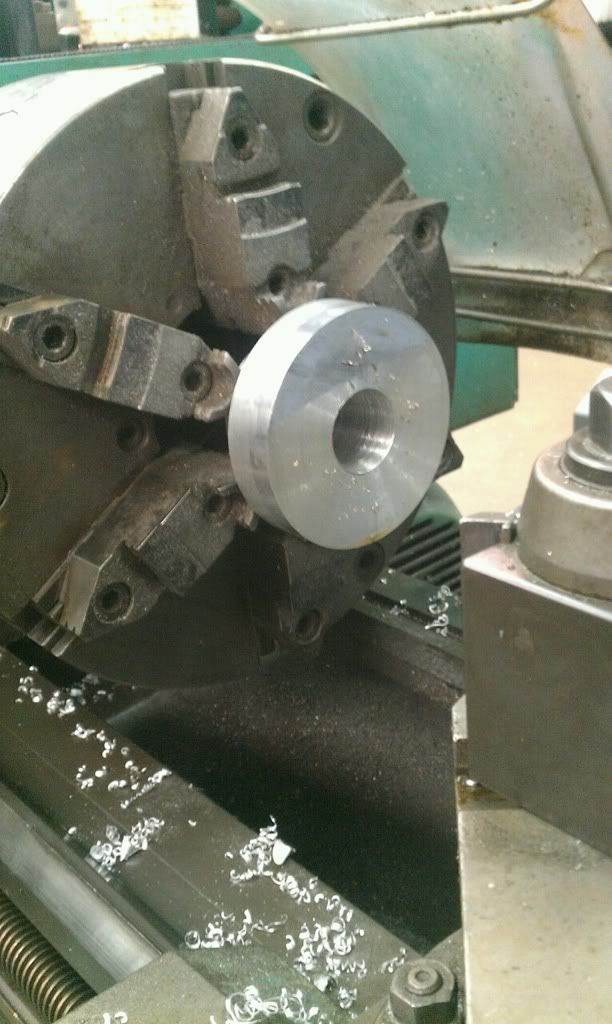

Posted:
Fri Mar 29, 2013 4:37 am
by bigpunn421
that seems like a huge waste of metal and energy. but i guess your learning so its ok.
i would try the method i posted if you can do it safe. get a 3" tube and put it in lathe and use some leverage to mold the funnel shape.
but post pics when its done i would like to see it and its measurements

Posted:
Fri Mar 29, 2013 4:48 am
by 92civicEGsedan
bigpunn421 wrote:that seems like a huge waste of metal and energy. but i guess your learning so its ok.
i would try the method i posted if you can do it safe. get a 3" tube and put it in lathe and use some leverage to mold the funnel shape.
but post pics when its done i would like to see it and its measurements
I got the metal for free and Im making it to pass time in my class I'm tired of making shifters

Posted:
Thu Apr 11, 2013 1:18 am
by 92civicEGsedan
Velocity stack is now finished but I want to change the inside lip radius to something bigger

Posted:
Thu Apr 11, 2013 4:30 am
by 92civicEGsedan

Posted:
Thu Apr 11, 2013 4:31 am
by 92civicEGsedan